In the world of water treatment, corrosion is a major concern. If not controlled, corrosion can lead to poor energy transfer in heat exchangers, creation of favourable microbiological conditions in cooling towers, and even complete failures in steam boilers. Pipework, heat transfer surfaces and externals are all susceptible to corrosion.
Corrosion prevention in cooling towers
If cooling tower water isn’t properly treated, corrosion can occur. This happens when certain contaminants in the water, mainly gasses such as oxygen and carbon dioxide, cause the metal to degrade and return to its oxide state by means of an electrical or electrochemical reaction. This thins areas of the metal and increases chances of rupture.
Corrosion can be serious; it can lead to equipment failure, plant downtime, or the loss of heat transfer, and will contribute to conditions favourable to bacterial growth. Different types of corrosion commonly seen in cooling towers include:
- Pitting - This type of corrosion is extremely destructive as it is concentrated on small areas. It's also the hardest type to detect and can perforate metal in a short timeframe.
- General - This type of corrosion occurs evenly across the surface of the metal and can contribute to fouling and reduce system efficiency.
- Galvanic - This type of corrosion occurs when two different metals come into contact enough to conduct electricity. The electrical differences attack the more active metal, corroding it rapidly.
In addition to dissolved gasses, some other factors that can lead to corrosion in a cooling tower include:
- Bacterial contaminants.
- Variations in temperature.
- Alkalinity (pH).
- Dissolve and/or suspended solids.
Choosing not to treat the cooling tower water for these corrosion inducing contaminants can be costly and dangerous. Some solutions might include filtration, building the system with corrosion-resistant materials (such as stainless steel piping), and using chemical controls such as corrosion inhibitors and biocides.
Corrosion prevention in steam boilers
Boiler corrosion is the active destruction of sound boiler metal by the pitting action of dissolved oxygen in the boiler water.
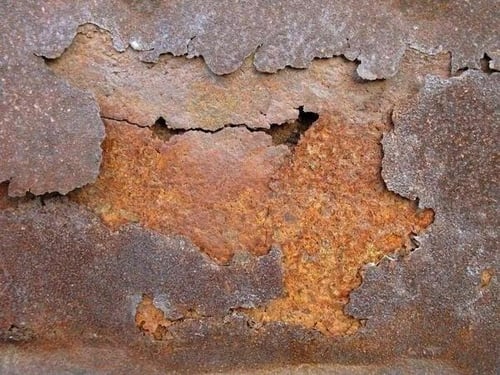
This usually results in deep holes in the metal which are self protected by further corrosion products, i.e. scabs or blisters, over the hole which allow the chemical reaction to continue.
Thus, generally large surfaces of the metal can be quite sound and yet an oxygen pitting site can develop deep penetration through boiler metal to cause ultimate failure.
The primary objectives in boiler design, operation and effective treatment include:
- Efficiency in heat transfer.
- Minimisation of energy usage.
- Production of pure steam.
- safe, reliable operation.
The problems encountered in steam-raising plants can be severe if scale formation and corrosion are allowed to occur. Problems can range from loss of efficiency and reduction of plant life to, at worst, catastrophic failure. It is also necessary to prevent boiler water carryover, where boiler water (including its dissolved solids) is carried into the steam, sludge deposition and foaming.
Both external and internal treatment of the boiler water is used for optimal operation. An effective internal boiler treatment programme involves the addition of chemicals to the feed water, boiler water and steam in order to confer desirable attributes, or to react with traces of undesirable constituents which can remain after external treatment.
Typically, oxygen scavengers, dispersants and alkalinity builders are standard. Other products including condensate line corrosion inhibitors and antifoams may also be used. B & V Chemicals offer a full range of treatment products for steam boilers.
Corrosion prevention in closed systems
The problems encountered in closed circuit systems are like those in open systems – corrosion, suspended solids, scale, and microbiological contamination.
However, there are differences between the systems which require us to treat them in different ways. The fixed volume, low make-up of a closed system allows us to dose water treatment products at much higher levels than is possible in open systems, where water is constantly lost to drain. Much better corrosion control can therefore be achieved in closed systems.
Another factor is that the dissolved oxygen level in a closed system should be low, which should reduce corrosion rates. Higher biocide levels and long contact times allow good microbiological control in closed systems to be achieved. Scaling is not generally a problem unless there is substantial make-up.
B & V Chemicals has a full range of scale and corrosion inhibitors, pre-commission cleaners, system flush chemicals, and biocides for use in closed circuit heating and chilled systems. This range also contains many specialist products formulated for use in specific specialist or problematic situations.
Our range of specialist, effective pre-commission cleaning, biocidal flushing and system flushing chemical formulations are outlined here.
Corrosion will be caused by the following.
- Oxygen
- Galvanic corrosion
- Microbiologically induced corrosion (MIC)
It is therefore important that closed systems are carefully monitored and regularly maintained to prevent corrosion and scaling occurring. Good corrosion protection is extremely important as the insoluble products of corrosion cannot be eliminated since there is no bleed off. These insoluble products form deposits in the system plugging lines and valves. Deposits also impede heat transfer thus increasing energy costs.
Closed systems are also prone to microbiological contamination by Pseudomonas, Nitrite reducing bacteria (NRB) and Sulphate reducing bacteria (SRB) which can result in severe waterside problems including degradation of inhibitors such as nitrite, local corrosion, gas generation and fouling by deposits.
A thorough testing regime alongside corrosion inhibitors suitable for the metallurgy of the system and biocides to maintain bacteria free systems are crucial to the longevity of the systems.